
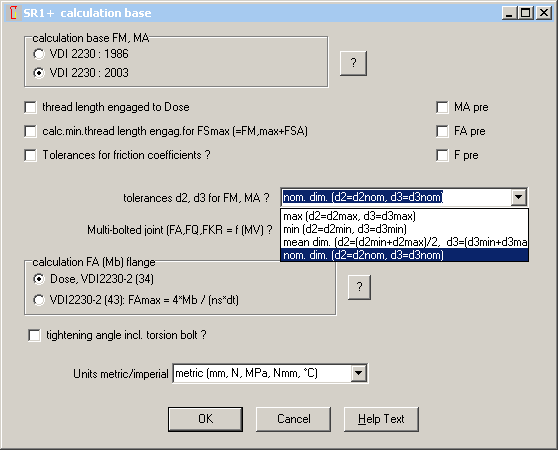
This is not how loads are applied on the joint, however, the simplest analytical model of a bolted joint is based on this assumption so I am curious to see how it compares with the FE model. In the first set, the external tensile load on the joint is applied directly to the bolt head while holding the nut. I have used two sets of boundary conditions. This is typically how I create 3D or beam element bolts in my professional work. The bolt to nut connection is bonded and the bolt has a straight shank (no fillets) with a cross-sectional area equal to the tensile area of the bolt.

The second simplified model does not include any threads. The only simplification, I have with regards to geometry is that the threads do not have a helix angle in order to make use of the axisymmetry model.
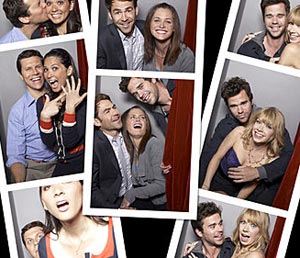
I also rounded sharp thread corners with small 0.3 mm radii since, in reality, no sharp corners exist and to prevent any stress singularity. Please note here that if you model the basic (ideal) thread geometry, there will not be any gap between the threads and the resulting stress distribution will not reflect reality. The threads are based on 6g/6H tolerance which is applicable for general use in commercial applications such as wind turbines. Additionally, the bolt geometry is realistic and includes tapered shank before the threads as well as fillet at the bolt head to shank corner. In the first or detailed model, threaded frictional contact is created between the nut and bolt. Finite Element Models of Bolted Connections
